Challenge
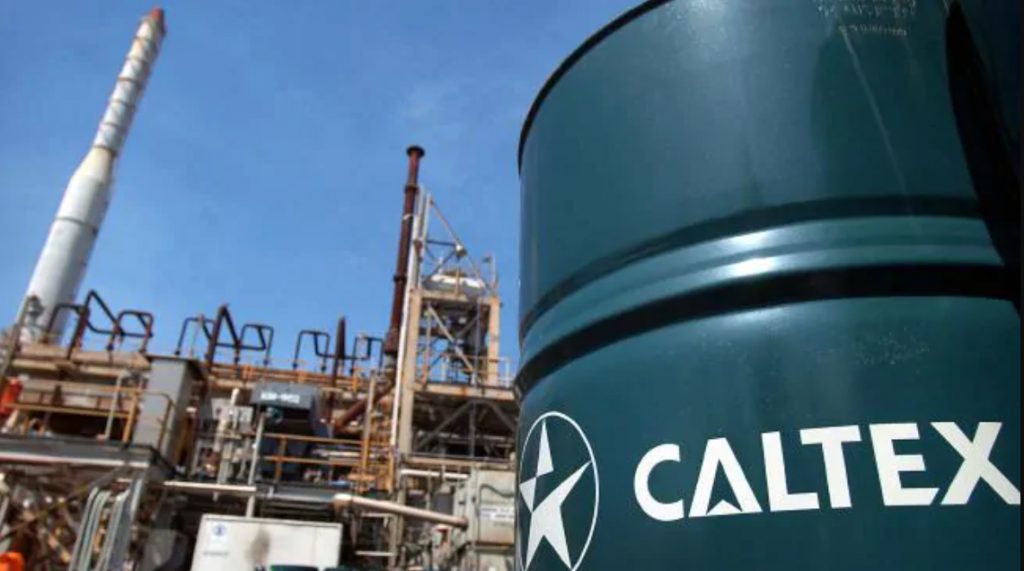
Issue:
The original seal that was being installed had a higher rate of deterioration because it was manufactured from Nitrile – a rubber synthetic compound that has lower temperature ratings.
Due to its custom size, the original seal that was installed had vulcanized joints. This ultimately means, the client ended up having a weaker seal.
As many seal manufacturing companies do not have the capability to manufacture seals at a larger scale (most seal companies have minimum run line of 15mm), moulds are being used. This would mean that the client will incur additional costs.
Solution
A large custom tank vessel seal with a dimension of 1.100mm which was made in one piece, with no vulcanized joints. The large seal was manufactured from Oz Seals own seal manufacturing systems that has the capability to manufacture seals with dimensions of up to 2000mm.
Manufactured from triple-lubricated Oz Super Polymer, the seal has excellent temperature characteristics and have proven itself in tough application situations. Due to its elasticity and flexibility of the Super Polymer, the large seal was easily packed, shipped and installed.
Despite the seal design having a higher level of intricacy and a larger dimension, the whole manufacturing process from start to finish took only 4 days (includes quality check, packing and shipping).
Results
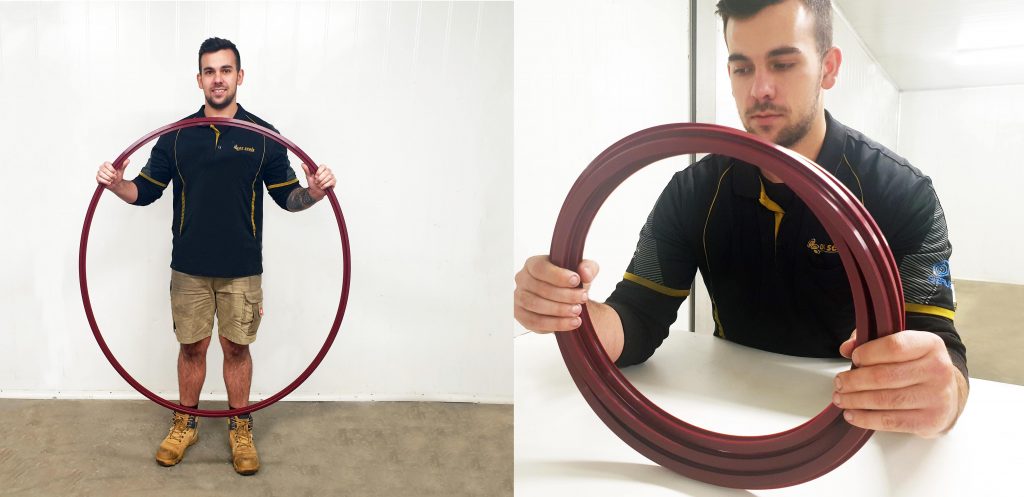
Client Reported:
- The custom tank vessel seal was easily installed and is running smoothly.
- Client is extremely satisfied with the seal as it is much stronger despite its working conditions and no signs of extrusions.
- Client is confident that there will not be any more breakdowns and application will continue to run smoothly for the next few years.