Challenge
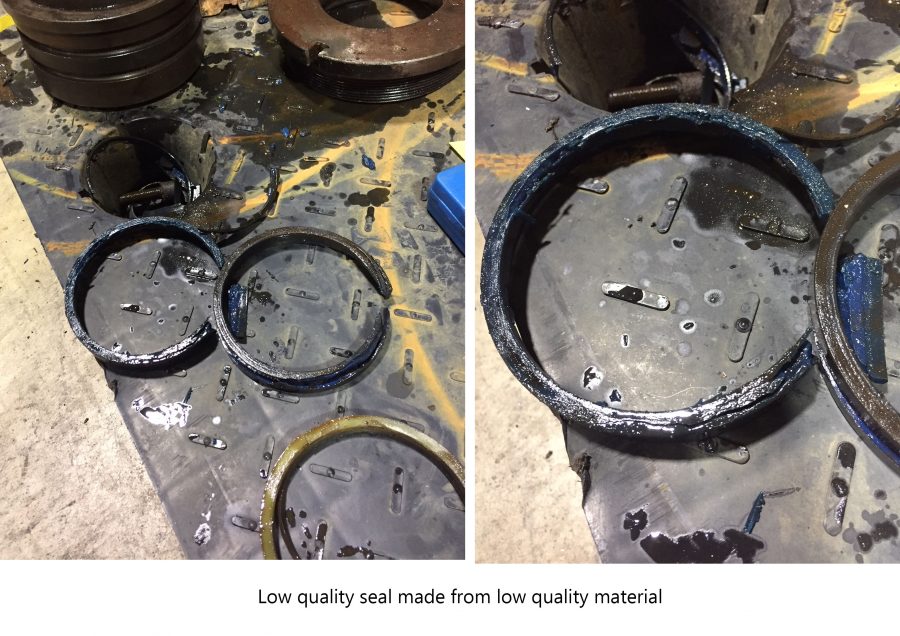
Issue:
Cheap and average quality seals are made from thermoplastic polymer. Client had a average quality injection-moulded seal that has melted and broke under the strain due to extreme temperature fluctuations (heating and cooling). Average quality seals last only for 3-6 years.
The problem with injection-moulded seals is when the temperature increases, they soften rapidly. This leads to extrusion and nibbling failure patterns in the seal. Injection moulding loses more than 20% of their properties when melted and injected.
Solution
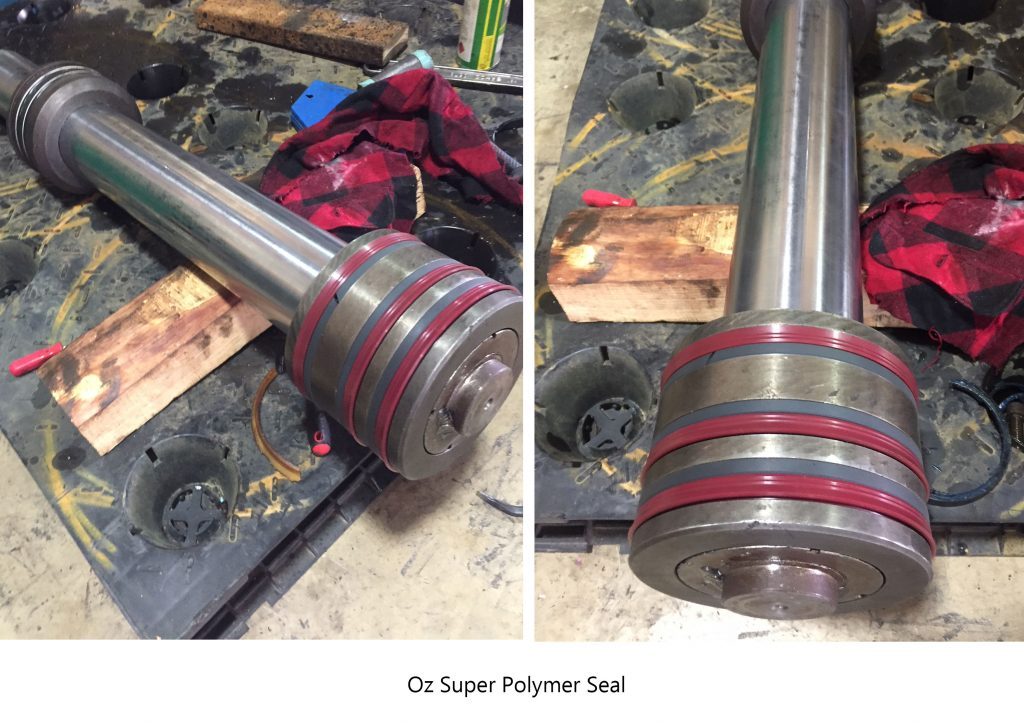
After having encountered many seal failures, Oz Seals has set the tone for the development of good quality and hard-wearing polyurethane seals. Using only high quality 100% virgin PU raw material to produce stable and void-free base seals.
The range of super polymers are thermoset and spin cast. They were made from the Oz Poly4 four-component processing plant which is an enclosed process that works in a controlled environment to prevent contamination.
This high-performance material is a triple, lubricated polyurethane that is able maximize its elasticity and is effective in fast operating cycles. These polymers have excellent temperature characteristics and have proven itself in tough application situations
Results
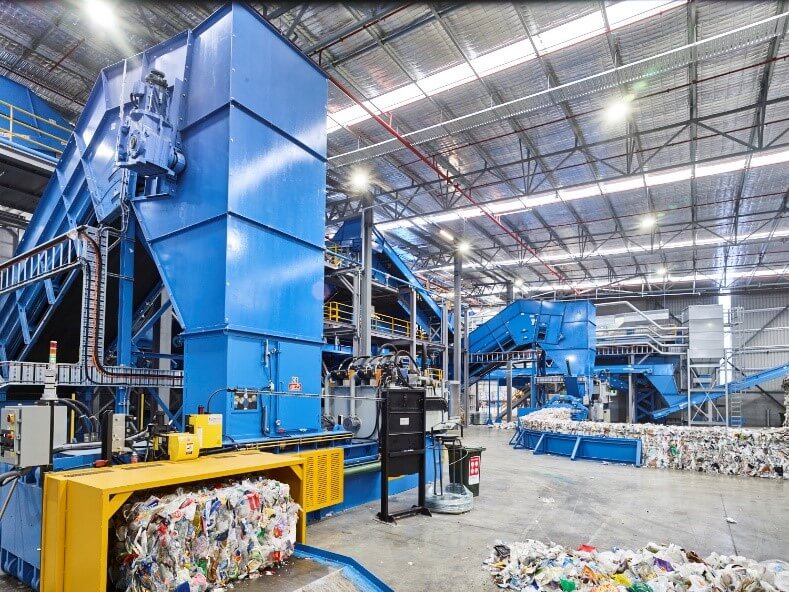
Client Reported:
- The super polymer seal is working well and is still continuing its service
- Performing extremely well in comparison to the previous seal.
- Savings realised due to production downtime, maintenance time and replacement.